PRODUCT SIZE
125x200x12.5mm
GEOLOGICAL PERIOD
Holocene - Cambrian
Present - 550 MYA
COMPOSITION
50% Portland Cement (limestone, clay, shale)
25% Filler (fly ash)
10% Cellulose (wood pulp)
15% Mica
125x200x12.5mm
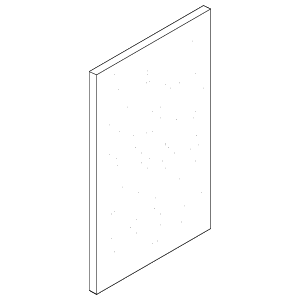
GEOLOGICAL PERIOD
Holocene - Cambrian
Present - 550 MYA
COMPOSITION
50% Portland Cement (limestone, clay, shale)
25% Filler (fly ash)
10% Cellulose (wood pulp)
15% Mica
GEOLOGICAL BIO
According to a manufacturer of fiber cement cladding, “These wood-look cement planks could fool the neighbors! After all, it’s all about putting up a good façade.” This particular mix of fine cement and cellulose fibers spans across hundreds of millions of years of geological eras (cement being limestone from the late Jurassic period), yet takes just 3 days to produce an optically convincing wood alternative. Being hard, homogenously flat, and receptive to adhesives and grout, fiber cement sheets are also invisibly installed as backer boards for tiles, wall cladding, and countertops.The infusion of cement with wood particles makes for "no-rot" boards that can be molded and coated in a vast range of colors, styles, surface effects, UV protection, even iridescence (reflex coating). Among popular residential products are natural-look wood siding boards, replete with "authentic" faux wood grooves that are “more elegant than [plastic] vinyl” and "Engineered for Climate®".
EXTRACTION / MANUFACTURING PROCESS
Dissolve bales of pulp in water ︎︎︎ mill to desired fineness ︎︎︎ add slurry in large vats ︎︎︎ add cement ︎︎︎ rotate cement-fiber-water slurry in cylindrical sieves ︎︎︎ wind product around format roll and push through cutting blade ︎︎︎ press panels under pressure to release extra water ︎︎︎ cement hardens and releases heat ︎︎︎ wait three weeks for setting OR bake in high-pressure autoclaves that steam and cure boards [energy-intensive] ︎︎︎ dry panels in oven ︎︎︎ color coating (optional) ︎︎︎ cut and finish ︎︎︎ pack and ship
According to a manufacturer of fiber cement cladding, “These wood-look cement planks could fool the neighbors! After all, it’s all about putting up a good façade.” This particular mix of fine cement and cellulose fibers spans across hundreds of millions of years of geological eras (cement being limestone from the late Jurassic period), yet takes just 3 days to produce an optically convincing wood alternative. Being hard, homogenously flat, and receptive to adhesives and grout, fiber cement sheets are also invisibly installed as backer boards for tiles, wall cladding, and countertops.The infusion of cement with wood particles makes for "no-rot" boards that can be molded and coated in a vast range of colors, styles, surface effects, UV protection, even iridescence (reflex coating). Among popular residential products are natural-look wood siding boards, replete with "authentic" faux wood grooves that are “more elegant than [plastic] vinyl” and "Engineered for Climate®".
EXTRACTION / MANUFACTURING PROCESS
Dissolve bales of pulp in water ︎︎︎ mill to desired fineness ︎︎︎ add slurry in large vats ︎︎︎ add cement ︎︎︎ rotate cement-fiber-water slurry in cylindrical sieves ︎︎︎ wind product around format roll and push through cutting blade ︎︎︎ press panels under pressure to release extra water ︎︎︎ cement hardens and releases heat ︎︎︎ wait three weeks for setting OR bake in high-pressure autoclaves that steam and cure boards [energy-intensive] ︎︎︎ dry panels in oven ︎︎︎ color coating (optional) ︎︎︎ cut and finish ︎︎︎ pack and ship